Services: | Prepared Meals Company |
Location: | Chicago, IL |
The Client
Founded in 2011, our client is a prominent ready-made meals delivery company based in the Chicago area. It provides fresh, dietician-approved and chef-prepared meals directly to customers’ doors that can be heated and ready to eat in minutes.
Schaumburg Specialties has enjoyed a productive working relationship with the company since 2019, when it first started purchasing our standard aluminum pan racks – and we have been providing bulk orders of both single and double aluminum pan racks, as well as customized and custom built equipment for them ever since!
Of course, when such a valued customer asked us to create a tailormade solution to help them with a unique production challenge, we were delighted to assist!
The Challenge
Our client offers more than 40 flexible weekly menu options, as well as smoothies and supplements, to its many thousands of customers all over the country – so it goes without saying that it has a lot of ingredients and meals to prepare!
Much of the company’s expansive production line is made up of state-of-the-art machinery which needs regular cleaning and maintenance to ensure that production efficiency and capacity remains at its peak and that strict food hygiene standards are adhered to.
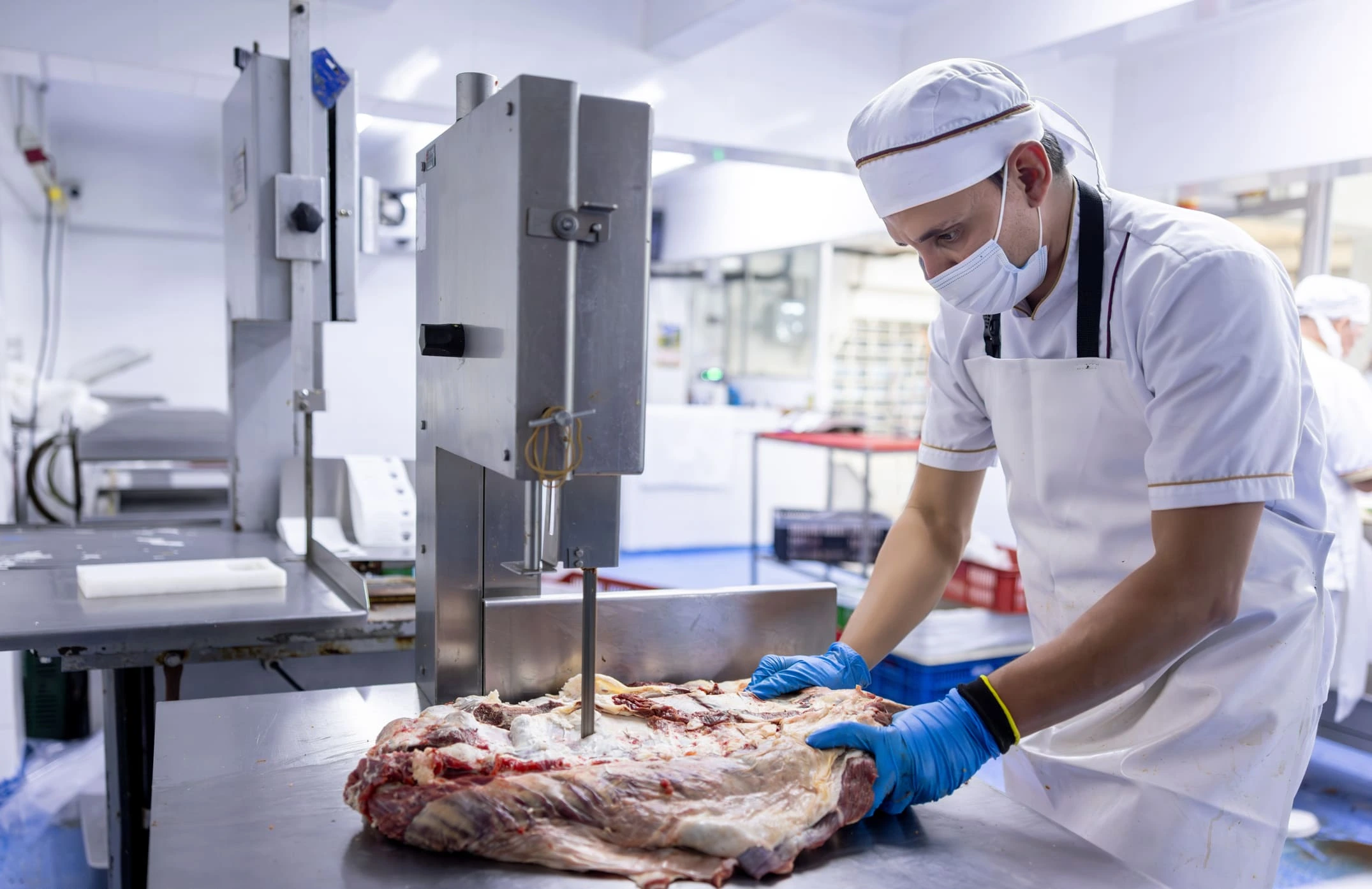
However, taking apart machines with lots of smaller pieces on a regular basis was causing problems. Employees needed somewhere to put the parts so they didn’t get lost or misplaced, mixed up or damaged while the rest of the machine was being cleaned. They also needed to be able to clean the smaller parts themselves and have somewhere to put those cleaned parts, before reassembling the machine in a speedy fashion, to minimize downtime and operational disruption.
Shadow boards are commonly used in food production and processing plants to house brackets, rings and other tools and parts while machinery is cleaned and sanitized, and our client’s way of working was no different. However, its production machinery was unique, so the boards and the carts we created to hold and transport them had to be custom built from the ground up!
Our Solution
Cup machine shadow boards – with corresponding carts
Our experts consulted and collaborated with our client to produce a perfect tailormade solution.
To create the shadow boards, we laid out all the parts relating to each machine (using photos provided by the customer) on a big sheet of white vinyl and ensured there was enough space for every piece. Then the boards were carefully and meticulously crafted by our expert fabricators according to the size and number of each machine’s parts.
Each shadow board part was meticulously crafted
After the shadow boards were complete, we created their partner carts. Each cart was approximately 4ft x 2ft, with the shadow board affixed at the most appropriate angle to hold its parts securely in place (in the case of the cup machine, the optimum angle was considered to be 45 degrees).
The cup machine’s shadow board was affixed at 45 degrees
Each cart was manufactured to include trays with perforated middle sections (and a perforated tray base too for the cup machine cart) that could be used to place machine parts on either for cleaning or for air drying once the parts had been cleaned elsewhere. The perforated mid section allowed for any excess water to drain off the parts, ensuring they were clean and dry before being placed back on the shadow board.
Perforated feature for water drainage
All metal parts – as well as all the carts – were manufactured from American, easy-clean, thick stainless steel at our plant in Schaumburg, IL. Being a food production facility, we had to ensure that our client’s equipment was compliant with the strictest food hygiene standards.
The carts were built from durable, thick stainless steel
Another big part of the project was making sure that our client’s employees could smoothly, safely and efficiently maneuver the shadow boards and carts around their facility. For that purpose, we built strong, sturdy all-welded carts and fitted them with double-wheeled, heavy duty casters that ensured effortless mobility and no danger of swaying or breaking and anything being dropped or broken.
Sturdy carts with double-wheeled casters
Once the boards and carts were ready, we shipped them immediately to the customer’s Chicago area facility, where they got to work helping with the cleaning and maintenance of its production machinery.
We soon had feedback from our client that it was delighted with the performance of its new equipment and that the boards and carts were really boosting production efficiency and reducing the amount of downtime necessary to properly dismantle, clean and reassemble machinery parts.
All part of the sterling service from Schaumburg Specialties!
Bring Your Custom Build Ideas To Life With Schaumburg Specialties!
We delivered awesome results for this customer, and now we want to do the same for you. To bring your design ideas to life and get started with your own custom build project that’s tailormade for your business, contact us today!